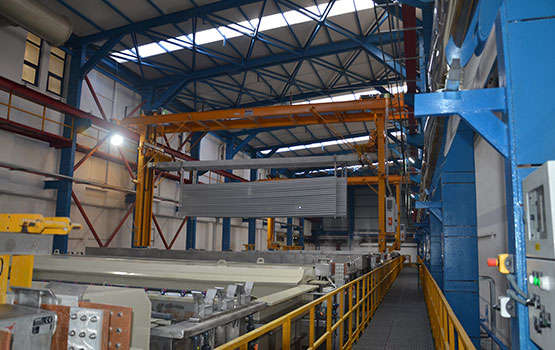
Aluminium is known as a durable metal with a very good corrosion resistance in most environments; however, untreated version of it may not have sufficent resistance to highly corrosive environments. In order to provide sufficient protection in such conditions, aluminium anodizing must be applied. Aluminium anodizing offers good abrasion resistance along with other superior properties while being quite hard. Anodic anodizing increases the thickness of the oxide layer formed on the aluminium to 10 - 25 microns from which is under normal conditions 1 - 2 microns while guarantees its’ resistance to highly corrosive environments as well as the decorative appearance Aluminium anodizing is mostly performed in an acid solution which is used as an electrolyte and coatings have thicknesses in the range of 1 to 100 microns depending upon the application,current density. The chemical formula of the layer coming out as a result of the anodic anodizing process on the alumina is Al2O3 The structure, which looks like an aluminium surface, por and barrier layer, can be of varying thicknesses, from 5 to 25 μm. These pores, which are formed in the future processes, are closed, compressed and transformed into corrosive environments and more resistant to heat. Even though the eloquence layer is intact, the pores formed must pass through a chemical process. There are two, mechanically and chemically, pre-treatments carried out for aluminium profiles prior to anodizing;
Mechanical Processes Prior to Anodizing
- Polishing: A special polish is applied to the surfaces to create a shinny profile surfaces by using polishing brushes.
- Satin Finishing Process: Aluminium profile is treated to obtain satin and matt finishing with brushes made of stainless steel waved wires by furnishing the surface with many lines.
Anodic Oxidation Process - Chemical Processes
- Degreasing: It’s aimed to clear away the dirts, oil and burrs on the profile surface with the degreasing process.
- Matt Anodizing: Aliminium surface is treated with liquid caustic to have a matte finish on it. Acid anodizing is an alternative way to the traditional caustic anodizing
- Neutralization: It is an acidic bath process used for removing coating defects on the aluminium surface following the process of chemical polishing and matting with caustic anodizing.
- Anodized coating: The rate of formation of the coating layer is 0.5 micron per minute, and sulfuric acid is used during aluminium anodizing.
- Coloring: The process of coloring is using for giving the surface of aliminium itself an aluminized color by immersing the aliminium surface with chemical agents right after having anodic coating as it resulting in porous structure. The part formed after the coloring process can be used for decorative purposes as well as for various purposes in some sectors. Treating the surface with cobalt sulphate in addition to the coloring gives a stabilitiy to the surface at a temperature of about 550°C.
- Sealing: Sealing is the last step of anodizing process and applied to the surface to close the pores on itself to give an aliminium resistance to chemicals and highly corrosive environments. The temperature, the puriy and cleanliness of the water used in the process and the chemical agents’ suitability (if it is used in it) are the parameters to be taken into consideration during this process. The the parts are left for drying after fixing to finish the aluminium anodizing process.
Chrome Nickel Plating
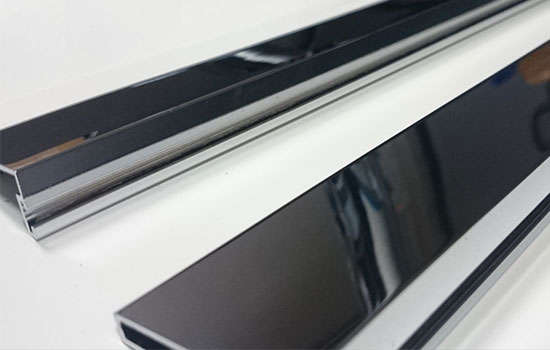
Chrome and nickel coating processes are carried out in Orego Metal with the latest technology. The nickel coating with a good interim decorative finish is noticeable with a smooth surface in mirror finish. Nickel, which should be perfect for your base metal polishing, is yellow and coated by our company to meet the needs of the companies. Nickelage is especially used in the construction of household appliances and in the decoration of steel parts of automobiles. For all goods exposing to the corrosive environments, nickel coating is usually applied before chromium coating.
Learn moreSandblasting / Brushing
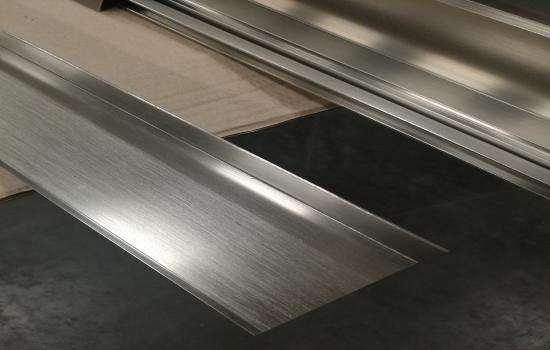
Aluminium Sanding is a process that applied to the aluminium surface with the purpose of cleaning, acquisition of texture or renovation. In order to ensure that the process takes place at a lower cost with the most efficient way, it is important to have the best possible understanding of the glazing principles. Thereby, we as Orego Metal think that it is a must to consider important issues like system components and sandblasting procedures in general. Aluminium sanding process is applied in the same way as the pressure system sanding process. The most basic elements in the pressurized system sanding process are; air compressor, compressed air desiccant, compressed air tank, sandblasting nozzle and pressure sandblasting boiler.
Learn more